Introduction to Applied Bearings
Applied bearings are pivotal components in a wide array of mechanical systems, playing a crucial role in reducing friction between moving parts and supporting rotational or linear movement. At its core, a bearing is a machine element that constrains relative motion, ensuring that motion occurs in a desired direction with minimal resistance. The primary function of bearings is to facilitate smooth and efficient operation of machinery, thereby enhancing performance and longevity.
The significance of applied bearings extends across various industries, including automotive, aerospace, manufacturing, and heavy machinery. In these sectors, the reliability and performance of bearings directly impact the efficiency and safety of operations. For instance, in the automotive industry, bearings are essential in the functioning of wheels, engines, and transmissions, ensuring smooth and reliable vehicle performance. Similarly, in the aerospace sector, high-precision bearings are critical for the safe and efficient operation of aircraft engines and control systems.
Understanding the fundamental principles behind bearing operation is essential for selecting the appropriate type for a specific application. Bearings operate on the principle of reducing friction by using rolling elements (such as balls or rollers) or by creating a thin film of lubricant between the moving parts. This reduces the contact area between surfaces, thereby minimizing wear and energy loss. Depending on the direction of the applied load and the operational requirements, different types of bearings are employed.
There are several types of applied bearings, each designed for specific contexts and performance criteria. Common types include ball bearings, roller bearings, and plain bearings, each offering unique advantages. Ball bearings, known for their versatility and low friction, are widely used in applications requiring high-speed operation. Roller bearings, which provide higher load-carrying capacity, are ideal for heavy-duty applications. Plain bearings, also known as bushings, are simple and economical solutions for applications with lower speed and load requirements.
In the following sections, we will delve deeper into the various types of applied bearings, their specific uses, and the best practices for maintaining them to ensure optimal performance and longevity.
Types of Bearings
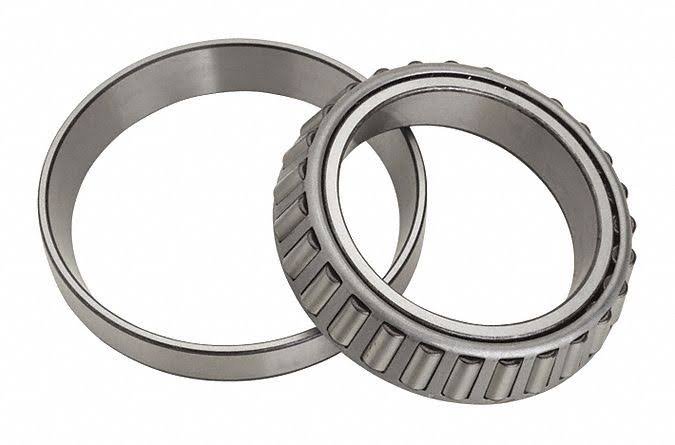
Understanding the different types of bearings is crucial for selecting the right one for your application. Bearings are essential components in various mechanical systems, designed to reduce friction and support loads. The most common types of bearings include ball bearings, roller bearings, and plain bearings. Additionally, specialized forms such as magnetic bearings and fluid bearings serve unique purposes in specific industries.
Ball Bearings: Ball bearings are widely used due to their versatility and efficiency. They consist of spherical rolling elements that minimize friction between the rotating and stationary parts. These bearings are typically found in applications ranging from skateboards to automotive wheels. Their primary advantages include low friction, high-speed capability, and durability. However, they may not be suitable for heavy load applications.
Roller Bearings: Roller bearings come in several configurations, such as cylindrical, spherical, and tapered. Unlike ball bearings, roller bearings use cylindrical or tapered rolling elements, which provide greater contact area. This design makes them ideal for heavy load applications, such as conveyor belt rollers and industrial machinery. While they offer higher load capacity, their design can lead to increased friction and wear over time.
Plain Bearings: Also known as sleeve or bushing bearings, plain bearings do not have rolling elements. Instead, they rely on a sliding motion between surfaces, which can be lubricated to reduce friction. Plain bearings are commonly used in applications like engine components and agricultural equipment. They are simple, cost-effective, and can handle heavy loads, but they may require more frequent maintenance due to wear.
Magnetic Bearings: Magnetic bearings utilize magnetic fields to levitate the moving part, eliminating physical contact and thereby reducing friction. These bearings are particularly useful in high-speed applications such as turbines and compressors. Their advantages include low maintenance and the ability to operate in extreme conditions. However, they are more complex and expensive compared to traditional bearings.
Fluid Bearings: Fluid bearings use a thin layer of liquid or gas to create a lubricating film between the surfaces. This type is often employed in high-precision applications like hard disk drives and high-speed spindles. The absence of metal-to-metal contact results in minimal wear and exceptional smoothness. On the downside, fluid bearings require a stable supply of fluid and precise engineering to maintain performance.
In summary, selecting the appropriate type of applied bearings depends on the specific requirements of your application, including load capacity, speed, maintenance, and cost. Each type of bearing offers unique advantages and potential drawbacks, making it essential to consider all factors before making a decision.
Materials Used in Bearing Construction
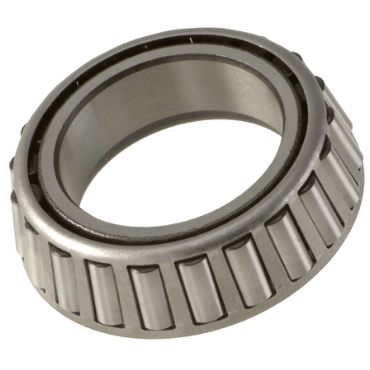
Applied bearings are constructed from a variety of materials, each selected for specific performance characteristics to suit different applications. The choice of material greatly influences the bearing’s load capacity, friction levels, wear resistance, and thermal properties. Common materials include metals such as steel and bronze, as well as non-metallic options like ceramics and plastics.
Steel is the most prevalent material used in bearing construction due to its robust characteristics. High-carbon, chrome, and stainless steel varieties are often employed because they offer excellent load-bearing capacity, durability, and resistance to wear and corrosion. However, steel bearings can be prone to rust if not properly lubricated and maintained, particularly in environments with high moisture levels.
Bronze bearings are another popular choice, especially in applications requiring good fatigue resistance and the ability to operate under heavy loads. Bronze’s inherent lubricity reduces friction and wear, making it suitable for high-speed applications. Its main downside is a higher cost compared to steel, which can be a limiting factor for some projects.
Non-metallic materials, such as ceramics, have gained traction in specialized applications. Ceramic bearings are lighter, harder, and more resistant to corrosion than their metallic counterparts. They perform exceptionally well in high-temperature environments and are less susceptible to thermal expansion. Despite these advantages, ceramic bearings are more brittle and expensive, which can be a drawback for some uses.
Plastics, including PTFE (Teflon), nylon, and UHMWPE (Ultra-High-Molecular-Weight Polyethylene), are also utilized in bearing construction. These materials are favored in applications where low friction, lightweight, and resistance to chemicals are critical. Plastic bearings are often used in food processing, pharmaceuticals, and other industries requiring high levels of hygiene. However, their load-bearing capacity and wear resistance are generally inferior to metal and ceramic bearings.
In conclusion, the selection of materials for applied bearings must consider the specific requirements of the application. Each material offers distinct advantages and disadvantages, making it crucial to balance factors such as load capacity, friction, wear resistance, and cost to achieve optimal performance.
Applications of Bearings in Various Industries
Bearings play a pivotal role in a multitude of industries, ensuring efficiency, performance, and reliability across various applications. In the automotive sector, applied bearings are integral to the operation of engines, transmissions, and wheels. For instance, wheel bearings facilitate smooth rotation of wheels, reducing friction and wear, which enhances the longevity and performance of vehicles. Similarly, engine bearings support the crankshaft, enabling it to spin freely and power the vehicle efficiently.
In the aerospace industry, the precision and reliability of bearings are paramount. Aircraft engines rely on high-precision bearings to withstand extreme conditions and high speeds. These bearings not only contribute to the optimal performance of jet engines but also play a crucial role in the safety and reliability of aircraft. For example, the use of ceramic bearings in jet engines helps reduce weight and increase fuel efficiency, while also offering resistance to high temperatures and corrosion.
The manufacturing sector benefits significantly from the application of bearings in machinery and equipment. Bearings are essential components in conveyor belts, gearboxes, and electric motors, ensuring smooth and efficient operation. In production lines, the use of high-quality bearings can mean the difference between seamless operation and costly downtime. For example, in a high-speed assembly line, precision bearings enable the smooth and rapid movement of parts, thereby boosting productivity and reducing maintenance costs.
In the medical devices industry, the application of bearings is crucial for the functionality and reliability of various equipment. Medical devices such as MRI machines, surgical robots, and dental drills rely on precision bearings for accurate and reliable performance. For instance, in surgical robots, miniature bearings allow for precise movements, enhancing the accuracy of surgical procedures and improving patient outcomes. Additionally, the use of corrosion-resistant bearings in medical devices ensures longevity and reliability in sterile environments.
Overall, the strategic application of bearings across these industries underscores their importance in enhancing operational efficiency, performance, and reliability. Whether in automotive engines, aerospace turbines, manufacturing machinery, or medical devices, bearings are indispensable components that drive innovation and productivity.
Common Issues and Failures in Bearings
Applied bearings are critical components in various mechanical systems, but they are subject to several common issues and failures that can lead to significant operational disruptions. Understanding these problems is essential for effective maintenance and prolonged bearing life. Key issues include wear and tear, corrosion, misalignment, and lubrication problems.
Wear and Tear: Over time, bearings naturally experience wear and tear due to constant friction and movement. The primary causes are inadequate lubrication, excessive load, and contamination. Symptoms of wear and tear include increased noise, vibration, and heat generation. If unchecked, it can lead to complete bearing failure, resulting in operational downtime and costly repairs.
Corrosion: Corrosion occurs when bearings are exposed to moisture, chemicals, or other corrosive substances. This issue is particularly prevalent in environments with high humidity or where bearings come into contact with water or corrosive chemicals. Corroded bearings may exhibit rust, pitting, and discoloration, which can compromise their structural integrity and performance. Preventive measures include using corrosion-resistant materials and ensuring proper sealing and lubrication.
Misalignment: Bearing misalignment happens when the shaft and bearing centerlines are not aligned. This can be caused by improper installation, deflection under load, or thermal expansion. Misaligned bearings often show uneven wear patterns, increased friction, and abnormal noise. Continuous operation under these conditions can lead to premature bearing failure. Regular inspection and alignment checks are crucial to mitigate this issue.
Lubrication Problems: Proper lubrication is vital for the smooth operation of bearings. Lubrication issues can arise from using the wrong lubricant, inadequate lubrication intervals, or contamination of the lubricant. Symptoms include increased friction, heat, and wear. Effective lubrication management involves selecting the appropriate lubricant, maintaining cleanliness, and adhering to recommended re-lubrication schedules.
Early detection of these common issues is critical for maintaining the integrity of applied bearings. Diagnostic methods such as vibration analysis, thermography, and regular visual inspections can help identify potential problems before they escalate. Addressing these issues promptly ensures the longevity and reliability of bearing systems.
Maintenance and Care of Bearings
Proper maintenance and care are crucial to ensuring the longevity and optimal performance of applied bearings. Routine maintenance tasks such as cleaning, lubrication, and inspection play a significant role in preventing common issues and prolonging the lifespan of bearings.
To begin with, regular cleaning is essential to remove any debris or contaminants that may accumulate on the bearing surfaces. Utilizing appropriate cleaning solvents and tools can help prevent damage during the cleaning process. It is vital to ensure that all cleaning agents are fully removed before re-lubrication to avoid any adverse reactions.
Lubrication is another critical aspect of bearing maintenance. It helps reduce friction, minimize wear, and protect against corrosion. Selecting the right lubricant, whether grease or oil, based on the bearing type and operational conditions is fundamental. Over-lubrication can be just as detrimental as under-lubrication, so it is important to follow the manufacturer’s guidelines regarding the quantity and frequency of lubrication.
Regular inspection of bearings for signs of wear, misalignment, or damage is also crucial. Visual inspections can identify issues such as discoloration, scoring, or unusual noise during operation. Using specialized tools like vibration analysis equipment can provide more detailed insights into the bearing’s condition, helping to predict potential failures before they occur.
Proper alignment and installation of bearings cannot be overstressed. Misaligned bearings can lead to uneven load distribution, increased friction, and premature failure. Ensuring that bearings are installed using the correct tools and techniques, as recommended by the manufacturer, will aid in maintaining their optimal functionality.
Finally, employing the right tools and adhering to manufacturer guidelines during maintenance tasks is paramount. Using incorrect tools or deviating from recommended procedures can cause more harm than good. Therefore, investing in proper equipment and comprehensive training for maintenance personnel can significantly enhance the effectiveness of bearing maintenance efforts.
By adhering to these practical maintenance tips, the lifespan and performance of applied bearings can be maximized, ensuring reliable and efficient operation across various applications.
Advancements in Bearing Technology
The field of applied bearings has seen significant advancements, driven by the need for increased efficiency, durability, and reliability across a myriad of applications. One of the most notable developments is the introduction of new materials. High-performance ceramics and advanced composites are increasingly replacing traditional steel bearings. These materials offer superior resistance to wear and corrosion, thus extending the lifespan of the bearings and reducing maintenance costs. In particular, ceramic bearings are gaining popularity for their lightweight properties and ability to operate under extreme temperatures.
Improvements in design and manufacturing processes have also played a crucial role in the evolution of bearing technology. Precision engineering and advanced manufacturing techniques, such as additive manufacturing (3D printing), have enabled the production of highly customized bearing solutions. These innovations allow for greater design flexibility, tighter tolerances, and enhanced performance. Additionally, the use of computer-aided design (CAD) and finite element analysis (FEA) has streamlined the design process, resulting in bearings that are optimized for specific applications and operational conditions.
The integration of smart technologies is another groundbreaking advancement in the realm of applied bearings. Sensor-equipped bearings, often referred to as “smart bearings,” are now capable of real-time monitoring and data collection. These sensors can track critical parameters such as temperature, vibration, and load, providing valuable insights into the bearing’s performance and health. This data can be used to predict failures, schedule maintenance, and improve overall system efficiency. The adoption of the Internet of Things (IoT) and Industry 4.0 principles further enhances the potential for predictive maintenance and automated monitoring systems.
Looking ahead, the future of bearing technology appears promising, with ongoing research and development focused on enhancing material properties, refining manufacturing techniques, and expanding the capabilities of smart technologies. These advancements are expected to have a profound impact on various industries, from automotive and aerospace to manufacturing and renewable energy. As the demand for more efficient and reliable bearing solutions continues to grow, the innovations in applied bearings will play a pivotal role in driving industrial progress and operational excellence.
Selecting the Right Bearing for Your Needs
Choosing the right bearing for a specific application is a critical step in ensuring optimal performance and longevity of your machinery. Several factors must be taken into account to make an informed decision, each playing a pivotal role in the bearing’s effectiveness and durability. Understanding load capacity, speed, environmental conditions, and cost are fundamental to making the right selection.
Firstly, assess the load capacity. Bearings are designed to handle different types of loads, such as axial, radial, or a combination of both. It is essential to determine the maximum load the bearing will experience in your application. Overloading a bearing can lead to premature failure, so selecting a bearing with an appropriate load rating is crucial.
Next, consider the operational speed. Bearings have maximum speed ratings that should not be exceeded to avoid overheating and wear. High-speed applications require bearings with low friction and precision tolerances to minimize heat generation. Conversely, for low-speed applications, bearings with higher load capacities and robustness may be more suitable.
Environmental conditions also play a significant role. Factors such as temperature, humidity, and exposure to contaminants like dust or chemicals can affect bearing performance. For example, in high-temperature environments, bearings with special lubricants and heat-resistant materials are necessary. Similarly, sealed or shielded bearings are recommended for dusty or contaminated environments to prevent debris ingress.
Cost is another vital consideration. While it might be tempting to opt for cheaper bearings, it is important to weigh the long-term costs. Investing in high-quality bearings can reduce downtime, maintenance costs, and extend the machinery’s lifespan, providing better value over time.
To streamline the selection process, follow a step-by-step approach:
1. Identify the application requirements, including load, speed, and environmental conditions.
2. Review technical specifications and compare them with your needs.
3. Consult with bearing experts or manufacturers to validate your choice.
4. Consider real-world scenarios and potential challenges to ensure the bearing will perform under actual operating conditions.
By carefully evaluating these factors and seeking expert advice, you can select the most suitable applied bearings for your needs, ensuring reliability and efficiency in your machinery operations.